Table of Content
1 What is Investigation in Pharma?
2 Types of Pharmaceutical Investigations
3 Guidelines for Investigation in the Pharmaceutical Industry
4 Best Practices for Investigating Issues in the Pharma Industry
5 Challenges in Pharma Investigations and How to Overcome Them
6 Close Pharma Investigations Faster & Smarter with Qualityze
Why choose Qualityze Inspection Management?
8 Concluding thoughts!
Why Qualityze?
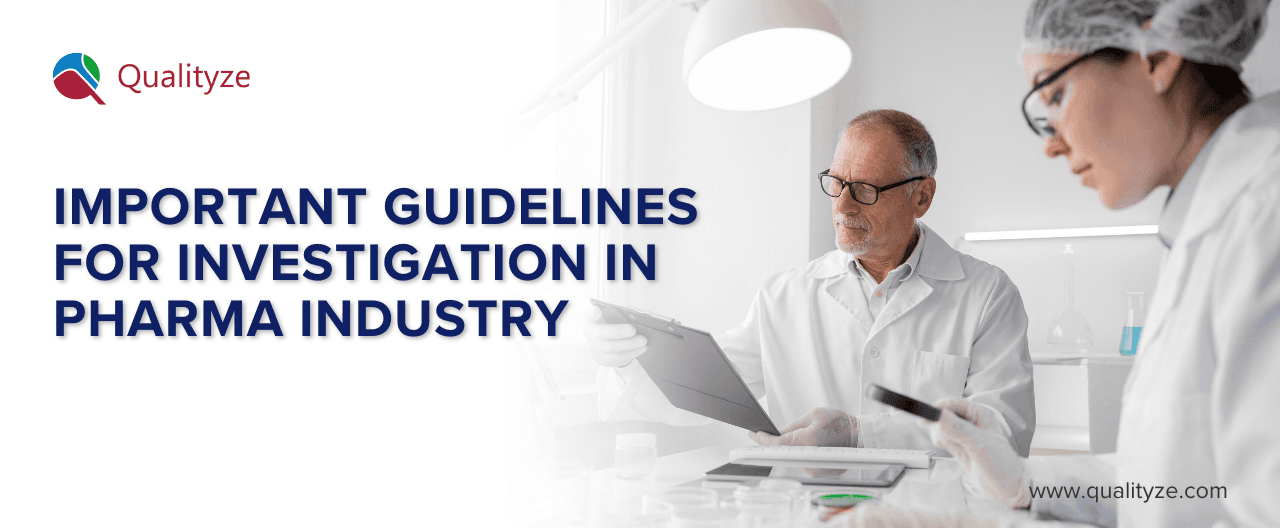
In the pharmaceutical industry, even minor anomalies aren’t just warning signs—they become immediate triggers for compliance action demanding a swift structured Investigation. When human health is on the line, there’s absolutely no room for error. Every deviation, whether it’s a process hiccup or an unexpected test result, demands prompt and structured Investigation.
These Investigations aren’t just to keep regulators happy; they’re central to maintaining product quality, upholding patient safety, and preserving your organization’s reputation. With regulatory bodies increasing scrutiny everywhere, pharmaceutical companies must be equipped to detect, investigate, and resolve issues swiftly and efficiently.
With human lives at stake, even the slightest deviation in pharmaceutical processes demands a swift, structured Investigation. Investigations in pharma are not just regulatory mandates—they’re the foundation of product integrity, patient safety, and brand credibility.
As regulatory scrutiny increases globally, organizations must be better prepared to detect, investigate, and resolve issues with precision and speed. In this blog, we explore what pharmaceutical Investigations entail, the different types, best practices, common challenges, and how leading pharma companies are leveraging digital tools to streamline their Quality Management Systems (QMS)
Let’s uncover the roadmap to a faster, more compliant approach to Investigations in pharma—and how Qualityze can support this transformation.
In this blog, we shall explore the fundamentals of pharmaceutical Investigations, their types, regulatory guidelines, best practices, and how digital solutions like Qualityze can help close Investigations faster—ensuring compliance, quality, and patient safety.
What is Investigation in Pharma?
Pharma Investigation is a formal, documented process that tries to find out the underlying cause of manufacturing deviations, defects, or non-conformances, quality control, or distribution. It is a key process for ensuring product safety, keeping GMP compliant, and eliminating future possibilities.
Whereas general troubleshooting is rather unstructured, pharmaceutical Investigations tend to operate within a formal system, frequently regulated by guidelines such as FDA 21 CFR Part 211 and EU GMP Annex 1. Regardless of whether the problem is a batch failure, out-of-specification test result, or customer complaint, the objective is to identify why it occurred and how to avoid future occurrences.
Investigations generally involve event recording, root cause analysis (RCA), risk analysis, impact analysis, and corrective and preventive actions (CAPA) implementation. The results provide feedback for process improvement, training maintenance, and even product recall if required.
Did you know? "FDA guidelines recommend initiating an Investigation within one business day of identifying an out-of-specification (OOS) result."
Good Investigation procedures aren't solely about preventing penalties—they're about promoting operational excellence in pharma.
Types of Pharmaceutical Investigations
Knowledge of the types of pharmaceutical Investigations is important in establishing the correct procedures, allocating roles, and maintaining compliance. Each type has different regulatory requirements, documentation types, and resolution processes.
Here are the most common Investigation categories:
- Deviation Investigations: Initiated by any deviation from authorized SOPs or batch records.
- Out-of-Specification (OOS) Investigations: Started when results are outside of specified acceptance criteria during quality control testing.
- Out-of-Trend (OOT) Investigations: Target identification of trends that are outside of historical data, though values may be within spec.
- Environmental Monitoring Investigations: Done in the event of contamination incidents or cleanroom breaches.
- Customer Complaint Investigations: Initiate when consumers, healthcare practitioners, or regulators bring forward a product-related issue.
Each type of Investigation needs to have a standard documentation trail, with RCA, CAPA linkage, and QA monitoring. Timelines are crucial—unresolved or delayed Investigations can cause 483 observations or warning letters. Correct categorization results in quicker resolution and more robust audit preparedness.
Guidelines for Investigation in the Pharmaceutical Industry
Investigation guidelines are grounded in global standards like ICH Q10, FDA 21 CFR Part 211, EU GMP, and WHO GMP. Adhering to these ensures traceability, consistency, and audit preparedness.
Core guidelines include:
- Timely Initiation: Start Investigations within 24 hours of the discovery of a quality event.
- Detailed Documentation: Document about who, what, when, where, and how for each incident.
- Structured Root Cause Analysis: Apply standard tools such as 5 Whys, Fishbone, or FMEA to identify systemic root causes.
- QA Review: All reports of Investigation should be approved and signed by the Quality Assurance unit.
- Linkage to CAPA: Root cause conclusions should be corrected through corrective and preventive actions.
- Data Integrity (ALCOA+): Make sure that the records are Attributable, Legible, Contemporaneous, Original, Accurate, and Complete.
- Closure Schedules: Investigations must be done within 30 days with written explanations for delays.
Following these guidelines mitigates compliance risks, enhances quality control, and supports continuous improvement efforts.
Best Practices for Investigating Issues in the Pharma Industry
Embracing best practices for investigating pharma issues ensures that Investigations are not only compliant but also efficient and effective.
Here are the top strategies:
- Establish Cross-Functional Teams: Engage QA, production, R&D, and validation experts for balanced RCA.
- Standardized Templates: Utilize pre-approved templates for every Investigation report to ensure consistency.
- Automation through QMS: Switch from paper-based records to electronic Investigation systems.
- Training: Provide regular training on deviation management, root cause tools, and documentation integrity.
- Digital Audit Trails: Keep total edit histories and e-signatures for traceability.
- RCA Tools: Apply 5 Whys, Fishbone diagrams, and Pareto analysis for systematic problem-solving.
- CAPA Monitoring: Monitor implementation timelines, ownership, and effectiveness using dashboards.
Did You Know? "Pharma Investigations can cut cycle times by 40% when they're digitized and become more audit-ready."
By incorporating these best practices, companies establish a culture of accountability and quality-driven decision-making.
Challenges in Pharma Investigations and How to Overcome Them
Even with checklists and SOPs, pharma businesses continue to struggle significantly with conducting Investigations in an effective way. Proactively addressing these is crucial to ensure regulatory compliance.
Common challenges include:
- Incomplete or inconsistent documentation
- Investigation delays in starting
- Unclear or unsubstantiated root cause findings
- Ineffective CAPA implementation or follow-up
- Human mistakes and limitations of manual tracking
How to overcome them?
- Automate and apply Investigation workflows using a strong QMS such as Qualityze
- Standardize RCA methods throughout departments to enhance consistency
- Real-time dashboards to monitor Investigation progress, bottlenecks, and escalations
- Regular training and audits to detect execution gaps
- Establish metrics such as closure rates, CAPA success, and repeat deviations
A structured digital approach can considerably decrease delays and mistakes, leading to improved compliance results.
Close Pharma Investigations Faster & Smarter with Qualityze
When it comes to closing pharma Investigations faster, Qualityze provides a best-in-class digital platform designed for highly regulated environments.
Why choose Qualityze Inspection Management?
- Pre-built configurable workflows tailored for deviations, OOS, and complaints
- Integrated RCA and CAPA tools with audit trail and traceability
- Automated alerts and task assignments for timely action
- Role-based dashboards to track performance across facilities
- Compliant with FDA 21 CFR Part 11 and EU Annex 11 regulations
Customer Impact:
A multinational vaccine firm improved deviation closure by 46% by deploying Qualityze Inspection Management at all sites.
Did you know? "Pharma manufacturers on Qualityze found their Investigation cycle time efficiency increased by 50% within the first six months."
From initiation to closure, Qualityze assists you in gaining control, boosting efficiency, and staying audit-ready—step by step.
Concluding thoughts!
Wrapping up here... Let’s be real, pharma Investigations aren’t optional busy work anymore. With regulations getting tougher, you need a process that’s streamlined and reliable, not just cobbled together. Throughout this post, we’ve zeroed in on the essentials: why tight Investigations matter, what best practices look like, and how a smart system can turn chaos into order. If your QMS is still stuck in spreadsheet mode, you’re leaving yourself open to risk.
As pharmaceutical Investigations become increasingly complex amid evolving regulatory demands, adopting a structured and efficient approach is no longer optional—it’s critical. Effective Investigations safeguard product quality, ensure compliance with global standards, and ultimately protect patient safety. This blog has highlighted the essential guidelines, best practices, and challenges faced in pharma Investigations, emphasizing how a modern QMS can transform these processes from cumbersome tasks into streamlined, audit-ready workflows.
Bottom line? Fast, structured, and traceable Investigations aren’t just buzzwords—they’re the cost of doing business in today’s market. You cut corners here, you end up paying for it later.
Why Qualityze?
Because a modern, cloud-based QMS enables smarter, faster, and more compliant Investigations. It centralizes documentation, automates workflows, and ensures your team stays audit-ready at all times.
Request a personalized Demo now to experience how Qualityze can streamline your pharmaceutical Investigations.
Visit us at https://www.qualityze.com/ for more insights on FDA- and EU-compliant QMS solutions. Empower your teams to investigate with precision, speed, and confidence—with Qualityze.
Want to reduce Investigation closure times, improve compliance, and digitally transform your pharma quality system?
Explore the Qualityze Inspection Management Solution now
Share
The Start of Something Amazing.
Request Demo
Products
Industries